1. Structure and application of mixing ring screw
The characteristic of the in-machine mixing ring
Screw barrel is that the mixing element is set at the position of the metering section, which mainly plays the role of mixing and homogenization. Based on the consideration of the mechanical manufacturing process, there are generally two forms in the structure, namely the pin type and the barrier type.
vertical machine screw assembly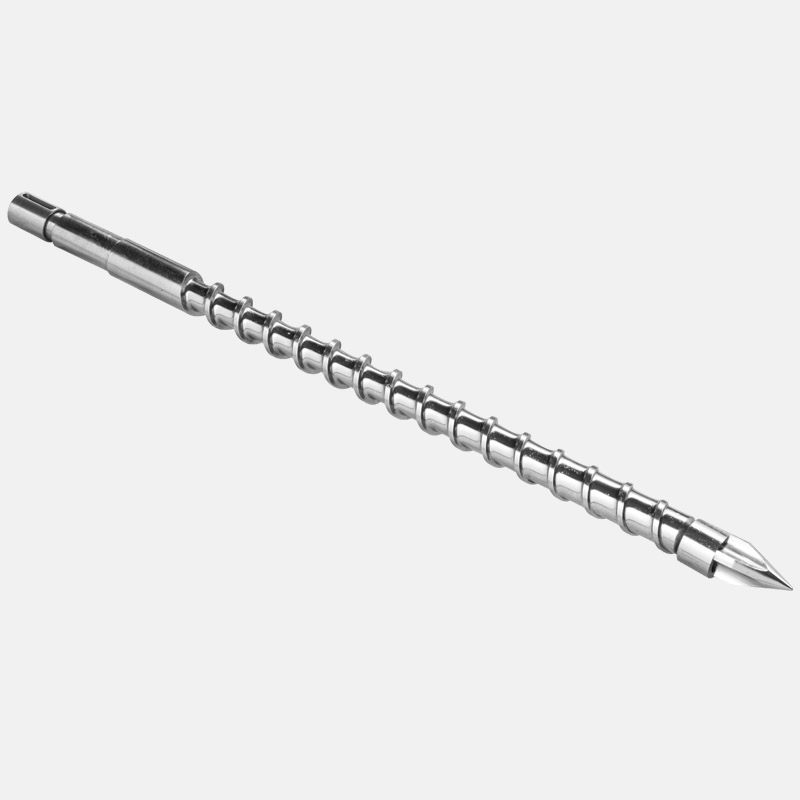
During the plasticizing process, the pin-type mixing element makes full use of the shunting effect of the pin. During the shunting process, the tiny fragments that have not been plasticized in the previous section will continuously absorb heat from the molten material, so that the entire molten material temperature drops. When the plastic passes through the pin, the solid phase in the material is pulverized and refined, and the melting time is shortened. And due to multiple times of mixing, plasticized melt can be obtained. This structure is more suitable for raw materials that require high temperature control and small temperature rise during processing. Such as HPVC, PET transparent material, etc. In the design, attention should be paid to the selection of parameters such as the position, quantity and circulation area of the pins.
During the plasticizing process, the barrier type mixing element can further homogenize the remaining unplasticized tiny fragments by using the shearing effect of the barrier edge between the feed chute and the discharge chute on the material, and at the same time the material can also be mixed. With this structure, the material should contain a certain amount of solid phase material before entering the mixing section, so as to maximize the efficiency of this element. Its color mixing and plasticizing effects are relatively good, but for some products with high transparency or raw materials with poor thermal stability, attention should be paid to the parameter selection of mixing components.
2. The structure and application of the separation screw
The structural feature of the separation screw is that an auxiliary flight is added in the melting section, and the main flight groove is divided into two parts. During the plasticization process of the screw, the solid-liquid phase separation is formed, and all the solid phase materials are left in the solid phase groove, while the solid phase The gas in the phase tank is discharged from the material backward under the action of pressure, which reduces the air bubbles in the product. At the same time, the heat exchange area between the solid phase material and the inner wall of the barrel is increased.
There are many structures of separate screw. In the actual design and test, our company believes that in terms of the convenience of machining and the effect of use, the lift of the main and secondary threads is equal, and the width of the liquid phase groove and the solid phase groove of the screw groove is equal. Keeping the same, the depth of the solid phase tank gradually becomes shallower from the compression section, while the depth of the liquid phase tank gradually becomes deeper until the end of the homogenization section. This structure is good for products with high transparency and raw materials with poor thermal stability. And the ability to adapt to raw materials is strong.
The design of the separation screw should reasonably select the screw parameters according to the actual situation, including the compression ratio, the distribution of the three sections and the position of the secondary screw flight.
3. The structure and application of double wave screw
The structural feature of the double-wave screw is that a parallel auxiliary flight is added to the groove of the single-wave screw, and the pitch is equal, the auxiliary flight is lower than the main flight, and the peak of one flight corresponds to the trough of the other. During the plasticizing process, not only the materials on the main and auxiliary screw flights are periodically sheared, but also the materials on the main and auxiliary screw flights can be continuously merged, which is conducive to homogenization, so compared with other screws, it can not only improve the plasticizing capacity , and can increase the mixing effect. It is suitable for injection molding of fillers, pigments, and foaming materials, and can obtain uniform components. It is also suitable for heat-sensitive materials such as HPVC, which can reduce degradation.