Co-rotating
Extruder screw barrel are used for compounding plastics, chemical processing, and food processing. Their modular design allows them to be configured for different tasks. They are mainly applied in reactive extrusion and graft modification of polymers.Co-rotating twin-screw machines are characterized by high output rates and flexibility. This makes them a very suitable machine for reactive extrusion. However, they also require good knowledge of material behavior.There are two types of co-rotating twin-screw extruders. These include the parallel and the intermeshing types. The parallel twin-screw extruder has two screws, which rotate in the same direction, while the intermeshing type has the screw elements arranged in such a way that the flight of one screw overlaps the root of another screw.In order to maximize extruder performance, it is important to sequentially position the screw elements along the screw.
Conical twin screw barrel for UPVC plastic pipe machine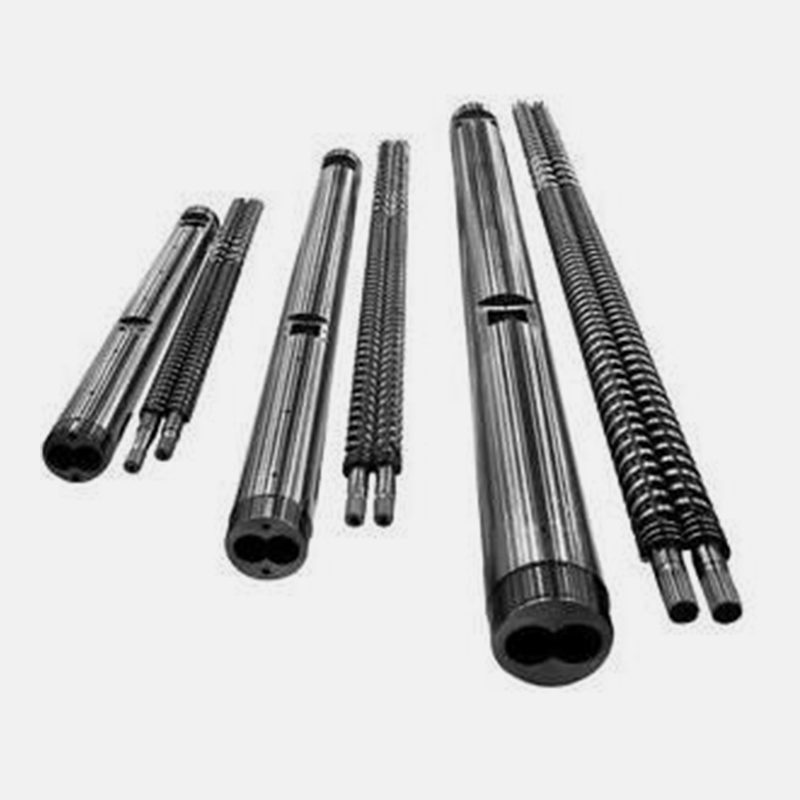
In order to achieve this, it is necessary to study the effect of input parameters.Single-screw extruders are widely used in the plastics industry. They are used to extrude plastic material and deliver homogenized melt to the die. The screw rotates to generate pressure to push the melt through the die. Depending on the design of the screw, the flow rate of the feed is either constant or variable.The screw geometry is typically characterized by a single metal ridge around the cylindrical root. The screw can be helical or multiflight. In some cases, the screw is cored in the feed zone, allowing internal temperature control.Single-screw extruders can be designed to extrude a wide range of materials. Some are particularly good for high filler content material. For example, powdered calcium carbonate is commonly used in the filling of plastics.Nonintermeshed twin-screw extruders have excellent mixing performance.
They can process solids, liquids and highly viscous materials. These systems can be used in several industries, including food, medical, and plastics.Several models have been developed for nonintermeshing screw extruders. One of these models focuses on the mixing efficiency of the entire system. Another model is more mechanistic. It considers the effect of one screw on another, as well as the effect of the geometry of the screw itself.A counter-rotating non-intermeshing twin-screw extruder is an excellent distributed mixing device. However, its disadvantages include high speed, a lack of pressure gradient, and low die pressure.Previous research has shown that the percentage of the channel filled is a good normalizing parameter for distributive mixing. In addition, larger extruders produce more mixing than smaller ones.The plasma arc is an intense beam of high energy that is used to weld metals together.
It can also be used to apply metallurgical deposits on the workpiece's surface.A special type of torch called a plasma welding torch is used in this process. Unlike lasers, plasma arcs are very efficient. They also have very good stability and melt depth control. Plasma welding is a suitable method for repairing thin metals.During the plasma welding process, a filler metal or alloy powder is melted and attached to the workpiece's surface. The fusion of the base material and the surfacing material produces an attractive bead with little or no ripple. This finish is very smooth, which makes finishing easier.The most popular alloy powders for powder plasma arc welding include composite powder and self-fusing alloy powder. These powders are commonly used because of their good performance and inexpensive price.